Volume 1, Year 2014 - Pages 38-48
DOI: 10.11159/jbb.2014.005
Increasing Ethanol Titer and Reducing Enzyme Dosage via Fed-Batch, Simultaneous Saccharification and Fermentation in a High Solids Bioreactor
Nichole A. Bauer,1 Craig C. Long,1 Bishnu Karki,1 and William R. Gibbons2
1Biology-Microbiology Department, South Dakota State University, Brookings, SD 57007, USA
2DBiology-Microbiology Department, South Dakota State University, Brookings, SD 57007, USA,
william.gibbon@sdstate.edu, 605-688-5499, (F) 605-688-6677
Abstract - Fed-batch, solid state, simultaneous saccharification and fermentation (SSF) was evaluated as an approach to reduce enzyme use in converting cellulose to ethanol, and to maximize ethanol titer. Kraft pulp, an intermediate in paper production, was used to represent a fractionated cellulose feedstock. Following a literature survey, average dosages were determined as 34 FPU of cellulase (Celluclast 1.5L) and 135 CBU of β-glucosidase (Novozyme 188) per gram glucan, and were set as 100% dosages. Initially, submerged fed-batch SSF trials were conducted in a traditional bioreactor using enzyme dosages of 17, 33, 67, and 133%, with a final solids loading rate (SLR) of 14%. Ethanol production was similar (77.3-83.4% of theoretical yield) for trials with 33-133% enzyme dosages, but fell to 36% of theoretical at 17% enzyme dosage. Fed-batch saccharification and fed-batch SSF were then performed in a solid state bioreactor, achieving a 34.8% SLR. This reduced the initial 133% enzyme dosage to 19%. In saccharification trials the glucose yield was only 35% of theoretical (103.6 g/L), due to feedback inhibition of enzymes. Companion SSF trials achieved an ethanol yield of only 20% of theoretical (30.1 g/L ethanol). While some ethanol was lost due to evaporation, yeast inhibition by low water activity was presumed to be the primary limitation. Performance at lower solid loading rates were evaluated, and even diluted the fermented slurry and conducted a secondary fermentation. These trials suggest that enzyme inactivation via irreversible binding may be the primary limitation, instead of low water activity or nutrient limitation.
Keywords: Saccharification, Cellulose, Ethanol, Solid state reactor, Fed-batch fermentatio.
© Copyright 2014 Authors - This is an Open Access article published under the Creative Commons Attribution License terms. Unrestricted use, distribution, and reproduction in any medium are permitted, provided the original work is properly cited.
Date Received: 2014-03-10
Date Accepted: 2014-09-03
Date Published: 2014-09-30
1. Introduction
Submerged bioreactors have traditionally been used for fermentation processes, including large scale systems common in corn ethanol facilities. Submerged bioreactors allow for precise control of temperature, pH, agitation, aeration, and mass transfer. The chief limitation is viscosity of the fermentation broth, as this limits mixing/mass transfer, and dramatically increases agitation energy requirements [1]. Thus, the solids loading rate in submerged bioreactors is limited by flow characteristics of the slurry and the forces exerted on the motor and impellers. Different types of solids can result in significantly different flow properties, even at the same solid loading rate [2]. For example, corn ethanol production typically employs >30% solid loading rate to achieve ethanol titers of >150 g/L. However because lignocellulosic biomass has a much lower bulk density, it is estimated that submerged bioreactors will only accommodate 10-15% solid loading, resulting in ethanol titers of 40-60 g/L [3]. These dilute, slurries will require substantially larger bioreactor volumes (and operational costs) along with greater energy input for ethanol recovery.
Another option for dealing with low bulk density feedstocks is to perform an initial saccharification of a dilute slurry, then remove the non-fermentable through filtration or centrifugation, and finally concentrate liquid through evaporation to achieve a clean solution with the desired sugar concentration for fermentation. One disadvantages of this method would be feedback inhibition of the enzymes during saccharification, resulting in incomplete sugar release [4, 5]. Also, if the non-fermentable solids are not washed, some sugar will be lost with these solids. The other major disadvantage of this approach would be the large amounts of energy necessary to concentrate the sugar solutions, especially if solids are washed.
An alternative to these methods is solid state conversion, in which a minimum amount of water is added, so simultaneous saccharification and fermentation (SSF) occur in the liquid film on solid particles [6, 7]. This would maximize solids loading and ethanol concentration, while minimizing energy needed for ethanol recovery [8]. There are many advantages of using a solid state fermentation system: lower production cost, less energy needed, and greater fermentation productivity [9]. Gibbons et al [10, 11] used solid state fermentation to convert sweet sorghum and fodder beet pulp to ethanol achieving ethanol yields of 85% and 78-85% of theoretical, respectively. Moukamnerd et al [9] used a solid state fermentation system to convert raw corn starch to ethanol. Ethanol was recovered continuously, with an ethanol yield of 93%. The purpose of the project herein was to compare submerged bioreactors versus solid state bioreactors at various solid loading rates of a cellulosic substrate. The goal was to minimize enzyme use, while maximizing ethanol production.
2. Materials and Methods
2.1 Enzymes, Yeast, Substrate, and Other Materials
Enzymes used in this study were obtained as a gift from Novozymes. Celluclast 1.5 L is a cellulase enzyme and has an activity of 4460.6 EGU/ml. Novozyme 188 is a β-glucosidase and has an activity of 18,150 CBU/ml. Enzymes were stored at 4 oC. Previously, we surveyed the literature and calculated the average dosage for Celluclast 1.5L (34 FPU /g glucan) and Novozyme 188 (135 CBU /g glucan) [12, 13]. These dosages were set to equal as 100%, and then we evaluated higher and lower enzyme dosages based on these literature values.
Saccharomyces cerevisiae NRRL Y-2034 was provided by the USDA National Center for Agricultural Utilization Research, Peoria, IL. For short term maintenance the yeast was stored on Potato Dextrose Agar Plates (PDA) plates and slants at 4 oC. Lyophilization was used for long term storage. Inoculum for all experiments was prepared by transferring colonies into a 5% glucose, 0.5% yeast extract broth (100 ml in 250 Erlenmeyer flasks), then incubating for 24 h at 35oC in a 250 rpm rotary shaker. Cell counts of the inoculum were nominally in the 3-6 x 108 CFU/ml range.
Kraft pulp was used as the substrate and was obtained as a gift from the Paper Science and Engineering Department at the University of Wisconsin - Stevens Point, and consisted of: 76.7% glucan, 0.5% arabinan, 7.7% xylan, 0.3% galactan, 6.7% mannan, and 3.2% lignin. The buffer solution consisted of 34.4 g sodium citrate per liter of distilled water. The pH was adjusted to 4.8 using 14 M HCl. A stock solution of tetracycline (10 µm/ml in 70% ethanol) was prepared and stored in the freezer. To control contamination, 5.3-6 ml of the tetracycline solution was added per liter of fermentation broth. Condensed corn solubles (CCS) was added as a low cost nutrient source for the yeast, and was obtained as a gift from a dry mill ethanol plant. Table 1 shows an analysis of CCS.
Table 1. Composition of Condensed Corn Solubles (CCS)
Parameters | As Received Basis | Dry Basis |
Total Moisture, % | 72.3 | 0 |
Total Dry Matter, % | 27.7 | 100 |
Crude Protein, Combustion, % | 5.25 | 18.9 |
Crude Fat (Diethyl Ether Extract), % | 5.71 | 20.6 |
Ash, % | 3.28 | 11.9 |
Fat: Roese Gottieb, % | 5.71 | 20.6 |
Crude Fiber, Crucible Method, % | 0.48 | 1.74 |
Nitrogen Free Extract, % | 13.0 | 47.0 |
Calcium, % | 0.03 | 0.10 |
Copper, ug/g (ppm) | 1.20 | 4.34 |
Magnesium, % | 0.22 | 0.80 |
Phosphorus, % | 0.46 | 1.66 |
Potassium, % | 0.77 | 2.70 |
Sodium, % | 0.20 | 0.74 |
Zinc, ug/g (ppm) | 29.9 | 108 |
2.2 Effects of Enzyme Dosage on Fed-batch Submerged SSF of Kraft Pulp
Trials in triplicate were conducted in a 5 L New Brunswick BioFlow III bioreactor to determine if fed-batch additions of kraft pulp could be made without the need for additional enzymes. The top portion of Table 2 lists the components initially added to bioreactors for treatments, resulting in final enzyme dosages of 17-133% of the literature average. Each bioreactor was also charged with 5.3 ml tetracycline solution, 10 g CCS and 20 ml of S. cerevisiae. The temperature was set at 35 oC and the agitation rate was initially set to 900 rpm so adequate mixing was achieved. After ~30 min the broth became less viscous, and the agitation rate was reduced to 75-100 rpm. The bottom portion of Table 2 lists the components added at 3, 6, and 24 h during the fed-batch process. The total volume of all trials was 2,856 ml, resulting in a total solid loading rate (SLR) of 14%.
Table 2. Materials for Fed-batch Submerged Fermentation
Materials Used | Treatment (Effective Enzyme Dosage) | |||
Components added initially | 133% | 67% | 33% | 17% |
Buffer (ml) | 1965 | 2127 | 2307 | 2364 |
Celluclast 1.5L (ml) | 216 | 108 | 54 | 27 |
Novozyme 188 (ml) | 240 | 120 | 60 | 30 |
Kraft pulp (g) | 100 | 100 | 100 | 100 |
Components added at @ 3, 6, and 24 h | ||||
Kraft pulp (g) | 100 | 100 | 100 | 100 |
Celluclast 1.5L (ml) | 54 | 27 | 0 | 0 |
Novozyme 188 (ml) | 60 | 30 | 0 | 0 |
Buffer (ml) | 0 | 0 | 114 | 114 |
2.3 Fed-batch Saccharification in a Solid State Bioreactor
To assess the performance of a solid state bioreactor we constructed, initial trials were performed in triplicate using fed-batch saccharification. The reactor (Figure 1) has a 16 L internal capacity with a horizontal shaft and paddles driven by a 0.373 kW variable speed motor (20-60 rpm). The reactor was placed within a static incubator for temperature control. The bioreactor was initially loaded with 1,380 ml of sodium citrate buffer, 54 ml of cellulase enzyme, 60 ml of β-glucosidase enzyme, 6 ml of tetracycline solution, and 100 g of kraft pulp. This provided an initial enzyme dosage of 133% and a SLR of 15%. The temperature was set to 35 oC instead of 50 oC, so the results would be more directly comparable to subsequent SSF trials. The agitation rate was set to 60 rpm, and saccharification was performed for 96 h. At 3, 6, and 9 h, 100 g of kraft pulp were added, and at 24 and 36 h, 200 g of kraft pulp were added, resulting in a final SLR of 34.8% and a final volume of 2,300 L. No additional enzymes were added, resulting in a final enzyme dosage of 19%.
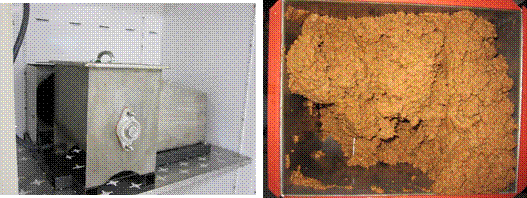
2.4 Fed-batch SSF in a Solid State Bioreactor
Initial fed-batch SSF trials were performed in triplicate following a similar protocol to that described above for fed-batch saccharification, except that all components were proportionally increased to achieve a final volume of 12 L. The second column of Table 3 lists the materials used in the 34.8% SLR trial and the final enzyme dosage. A 24 h yeast inoculum and CCS (to supply yeast nutrients) were also added initially.
Temperature and agitation were set to 35oC and 60 rpm, respectively, for the 96 h SSF. Due to inadequate conversion efficiency in the 34.8% SLR trial, presumably caused by low water activity, we gradually reduced the total SLR in subsequent trials as shown in the remaining columns of Table 3. We also tested a 14% SLR for comparison with the fed-batch SSF trials in the submerged bioreactor.
Table 3. Materials for Fed-batch Solid State SSF
Solid Loading Rates | |||||
Materials | 34.8% | 27% | 25% | 21% | 14% |
Cellulase (ml) | 282 | 70.5 | 65.28 | 54.84 | 36.56 |
β - glucosidase (ml) | 313 | 78.25 | 72.45 | 60.86 | 40.57 |
Buffer (ml) | 7020 | 1988.5 | 2059.52 | 2201.55 | 2450.12 |
Tetracycline (ml) | 31 | 7.75 | 7.75 | 7.75 | 7.75 |
Yeast (ml) | 120 | 30 | 30 | 30 | 30 |
CCS (ml) | 60 | 15 | 15 | 15 | 15 |
Kraft Pulp - initial (g) | 521.75 | 101.25 | 93.75 | 78.75 | 52.5 |
Kraft Pulp additions - 3, 6, 9 h (g) | 521.75 | 101.25 | 93.75 | 78.75 | 52.5 |
Kraft Pulp additions - 24 & 36 h (g) | 1043.50 | 202.5 | 187.5 | 157.5 | 105 |
Final Enzyme Dosages | 19% | 20% | 22% | 26% | 39% |
Total Volume | 12L | 3L | 3L | 3L | 3L |
2.5 Secondary Analysis of Fed-Batch, Solid State SSF Samples
To quantify the level of un-hydrolyzed cellulose remaining in the kraft pulp slurries at 0, 24, 48, 72, and 96 h, samples were collected and subjected to an additional saccharification. Each 5 ml sample of fermentation broth was blended with 89.3 ml of buffer in a stoppered, 250 ml Erlenmeyer flask. After autoclaving to kill the yeast, 2.7 ml of cellulase and 3 ml of β-glucosidase were added (133% enzymes dosage) to the cooled slurry, which was incubated at 250 rpm at 50 oC for 72 h. Glucose levels were determined by HPLC analysis at 0 and 72 h, and difference was used to calculate the amount of un-hydrolyzed cellulose present.
During the fed-batch SSF trials in the solid state bioreactor we noted high levels of glucose and lower levels of ethanol than we expected. We hypothesized that either nutrients or water activity may have limited yeast metabolism. Therefore samples were collected at 96h SSF and were subjected to the following tests. In one set of 500 ml Erlenmeyer flasks, varying amounts of buffer were added (10, 25, 50 or 100 ml) to 100 g quantities of fermented pulp to determine if water activity was limiting. In a separate flask, 49 ml of buffer and 1 g of yeast extract were added to 100 g of fermented pulp to determine if nutrients were limiting. These flasks were incubated an additional 72 h at 35oC in a rotary shaker (250 rpm), with HPLC analysis at 0 and 72 h.
2.6 Analytical Methods
Samples (5 ml) were removed at 0, 3, 6, 9, 12, 24, 36, 48, 72, and 96 h during the trials. To ensure sample uniformity, samples were collected with 10 ml wide mouth pipets. Samples were placed in sealed centrifuge tubes and boiled for five min to denature enzymes. Samples were the filtered through 0.2 µm filters into auto-sampler vials which were frozen until analysis. Carbohydrates, organic acids, and ethanol were measured in a Waters HPLC, with an Aminex HPX-87H column, and Waters 2410 refractive index detector. The mobile phase was 0.01 N H2SO4 at a flow rate of 0.6 ml per minute.
3. Results and Discussion
3.1 Effects of Enzyme Dosage on Fed-Batch Submerged SSF of Kraft Pulp
A 14% SLR of kraft pulp was used to evaluate fed-batch submerged SSF at enzyme dosages of 133, 67, 33, and 17% of the average listed in the literature. Based on the glucan content of the kraft pulp, the theoretical yields of glucose and ethanol were 120.9 g/L and 61.7 g/L, respectively. Figure 2 shows the average ethanol concentrations of these four enzyme dosages during the 96 h SSF period. Final ethanol titers of ~48-51 g/L were achieved with enzyme dosages of 133%, 67%, and 33%. These represented ethanol yields of 77-83% of theoretical and indicated that enzyme dosage could be safely reduced to 33% of the literature average (11.25 FPU cellulase and 45 CBU β-glucosidase per gram glucan). We do not have an explanation for the delayed ethanol production observed in the 133% enzyme dosage trial, but this trend was consistent for all replications. Maximum ethanol titer (22.23 g/L) and theoretical yield (36%) at the 17% enzyme dosage demonstrated that this level was insufficient for effective SSF.
Glucose concentrations during fermentation showed a typical early peak, since enzymatic saccharification rates initially exceed glucose consumption rates during the yeast growth phase (data not shown). After 24 h SSF, glucose levels were minimal, and final residual glucose levels were 0.43- 2.24 g/L in all trials. Cellobiose was not detected during SSF, while xylose (2.84-5.55 g/L) accumulated during fermentation, with higher concentrations in the higher enzyme dosage trials (data not shown). This was expected, since the S. cerevisiae strain Y-2034 cannot metabolize xylose [14].
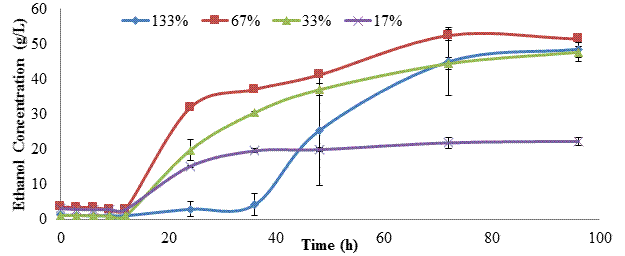
Table 4 lists the maximum ethanol titer, productivity, and residual glucose levels for these trials. As discussed above, the onset of ethanol production was delayed in the 13% enzyme dosage trial. This was correlated with a higher and more variable residual glucose titer. Thus it is possible that some unknown factor inhibited yeast metabolism in this treatment. These parameters are similar for enzyme dosages above 33%, showing that fed-batch SSF is an effective mechanism to reduce enzyme dosage [4, 15]. Kuhad et al. [4] also found that fed-batch feeding of substrate (de-inked newsprint) during SSF allowed an increase in SLR (from 2% to 6%), resulting in 14.78 g/L ethanol (85% yield) based on the 51% cellulose content of the newspaper. However, their final enzyme dosages (cellulase at 115% and β-glucosidase at 87% of the literature average) were significantly higher than used herein. Ballesteros et al. [15] used fed-batch feeding of recycled paper at 42oC to increase SLR from 5 to 10%. At a final enzyme dosage of 100% of the literature average for cellulase they obtained an ethanol yield of 79.7%. In the trials reported herein, enzyme dosage was reduced to 33% at a higher SLR (14%), and still achieved approximately the same ethanol yield (77%)
Table 4. Comparison of Yeast Performance at Different Enzyme Dosages during Fed-Batch Submerged SSF
Net Enzyme Dosage (% of literature average) | Maximum Ethanol Titer (g/L) | Ethanol Productivity (g/L/h)a | Residual Glucose (g/L) |
133 | 48.50 (± 3.5) | 0.51 (± 0.04) | 2.24 (± 1.66) |
67 | 51.42 (± 0.99) | 0.54 (±0.01) | 0.64 (±0.06) |
33 | 47.65 (± 1.6) | 0.50 (±0.02) | 0.43 (± 0.01) |
17 | 22.23 (± 1.1) | 0.23 (±0.01) | 0.49 (± 0.1) |
a At 96 hours |
3.2 Fed-batch Saccharification in Solid State Bioreactor
To determine if lower enzyme dosages would work at an even higher SLR (34.8%), fed-batch saccharification was conducted in the solid state, paddle type bioreactor. Initial enzyme dosages were 133% of the literature average, but since no additional enzymes were added during saccharification, the final enzyme dosage was 19% of the literature average. Incubation was conducted at 35oC instead of the normal 50oC so the results would be more comparable to subsequent SSF trials. Based on the solids loading and glucan content of the kraft pulp, the theoretical amount of glucose available was 296.1 g/L. Figures 3A and 3B show the saccharifiying mixture within the solid state bioreactor immediately before and after the third additions of 100 g of kraft pulp at 6 h. By 9 h the pulp liquefied sufficiently so that an additional 100 g of kraft pulp could be added. Similar trends of viscosity reductions occurred following the remaining kraft pulp additions at 9 h (100 g) and 24 and 36 h (200 g each). Thus the solid state bioreactor design was effective in mixing to at least 34.8% total SLR.
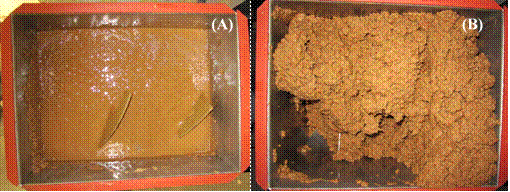
The maximum glucose level during saccharification was 103.6 g/L, which was achieved by 48 h, and represented 35% of the theoretical yield (Figure 4). Cellobiose levels also peaked at ~48 h, reaching 28 g/L. Dextrin (DP4) levels were relatively low (10-13 g/L) throughout. These finding were not unexpected, as it is known that cellulose deconstructing enzymes are inhibited by the build of up glucose and cellobiose [4, 5]. Low levels of xylose were expected, since kraft pulp contains low levels of xylan.
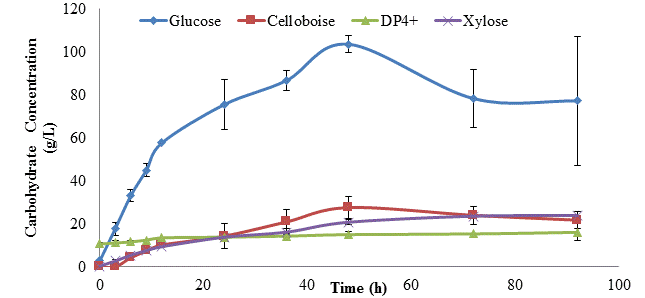
Using dilute acid pretreated corn stover, Rochel et al. [16] achieved 62% glucose yield after 96 h of batch saccharification (48oC) in a horizontal paddle-type reactor at a lower SLR of 20% (compared to 34.8% in our trials). Based on the literature average, their enzyme dosages were 28% for cellulase (Spezyme CP), compared to 19% in our trials. Jorgensen et al [17] achieved a 38% glucose yield after 96 h of batch saccharification of hot water treated wheat straw at 35% SLR, but their cellulase dosage was higher, at 25-40% of the literature average. Therefore, using a higher cellulose content feedstock, similar results to Jorgensen et al [17] were achieved at the same solids loading, but using half as much enzyme, and at a lower temperature.
3.3 Fed-batch SSF in a Solid State Bioreactor
Fed-batch SSF (following the same protocol as described above, except that S. cerevisiae was added at 0 h) was next conducted to assess whether conversion yields could be improved by continuously converting glucose into ethanol to minimize enzyme repression [8]. The first trial was conducted at a 34.8% SLR, with subsequent trials performed at SLR of 27, 25, 21, and 14% to reduce potentially adverse impacts of low water activity. Based on the glucan content of kraft pulp, the theoretical ethanol yield for the 34.8% SLR trial was 151 g/L, and progressively less for the other SLRs tested. Figure 5 shows the residual glucose levels, while figure 6 shows ethanol titers for these trials. Glucose levels rose during the first 12 h (yeast growth stage), but then fell as ethanol production began. However at 24 h in the 34.8% solid loading rate, glucose levels again began to rise, and continued to increase at approximately the same rate until peaking at 72 h (~70 g/L). This indicated that yeast metabolism was repressed, perhaps by the combination of low water activity and high ethanol titer [5]. In the other SLR trials, glucose levels fell to ~0 g/L by 96 h. Ethanol titers rose throughout incubation for all trials, then slowed as yeast metabolism was reduced. The highest ethanol titers of 48-50 g/L were obtained in the 25 and 27% SLR trials. This trend is also reflected in figure 7, which shows that ethanol yield in these trials was 42-44% of theoretical.
During the 96 h of SSF in the solid state reactor we noted a strong evaporative loss of ethanol. This was most noticeable during sample removal and addition of fresh kraft pulp, but because it was not possible to completely seal the lid of the reactor, ethanol was continuously volatilized. We believe this is the primary reason for the differences observed between the prior submerged SSF trial at 14% SLR (47.65 g/L ethanol, 77.2% yield at 33% enzyme dosage) and the comparable 14% SLR trial in the solid state reactor (30 g/L ethanol, 48.6% yield at 39% enzyme dosage). If this ~37% loss in ethanol is applied to the 25-27% SLR trials, maximal ethanol titers and yields would have increased to 67 g/L and 59%.
The kraft pulp slurry was monitored for un-hydrolyzed cellulose at 0, 24, 48, 72, and 96 h by subjecting samples to autoclaving (to kill yeast), followed by dosing with enzyme and conducting an additional 72 h saccharification. Significant levels of cellulose were present throughout SSF for all SLR trials (data not shown), along with the high glucose levels shown in the 34.8% SLR trial. Unfortunately, due to moisture loss (ethanol and water) from the solid state pulp during autoclaving, it was not possible to calculate the percent conversion of cellulose. However this demonstrated that cellulose hydrolysis was limited by some factor in the solid state SSF process.
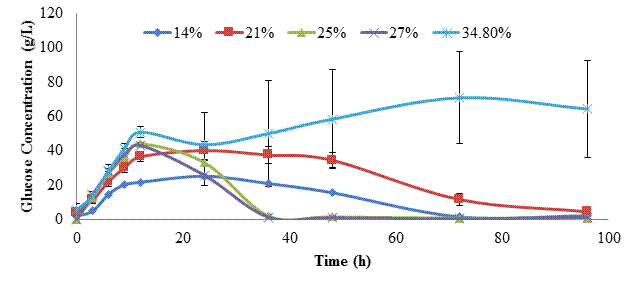
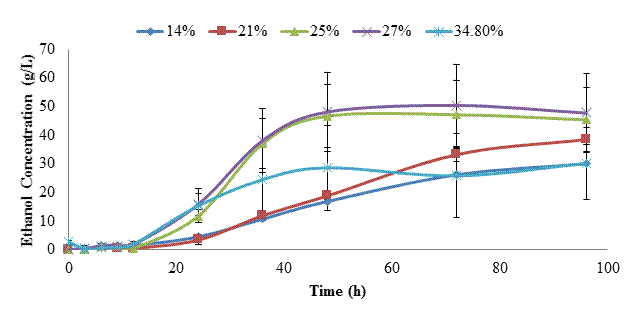
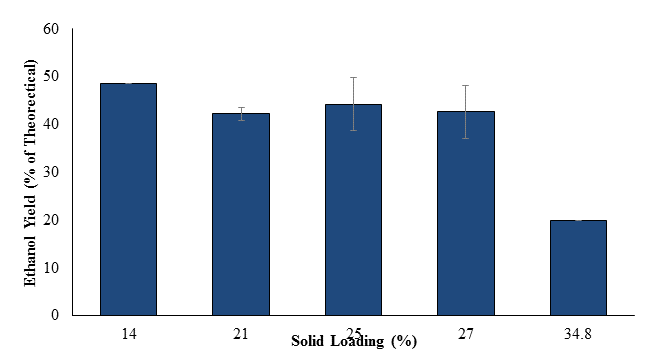
Jorgensen et al [17] conducted a separate hydrolysis (8 h at 500C) of hot water treated wheat straw at 35% solids loading, using enzyme levels of 34% of the literature average. After 144 h fermentation they obtained 39% of the theoretical ethanol yield, compared to the ~20% yield we obtained with a 19% enzyme dosage. Zhang et al [8] conducted fed-batch SSF of corncobs pretreated with dilute sulfuric acid, sodium hydroxide, and aqueous ammonia pretreatment or simple soaking in aqueous ammonia. At a final solids loading of 25% and using a cellulase dosage of 67% of the literature average, they obtained ethanol yields of 67.8%- 89%. This compares to the 44% yield (or 60% if corrected for ethanol evaporative loss) we obtained at 25% SLR, but required three times more enzyme than the 22% dosage we used at this SLR. Thus enzyme dosage appears to play an even more critical role at higher SLRs, likely due to the increased viscosity that would reduce mass transfer [18, 19, 20].
To further explore why ethanol yields were lower than expected during fed-batch SSF, 100 g quantities of the fermented slurry were mixed with 10, 25, 50, and 100 ml of buffer, and the flasks were incubated at 35oC for an additional 72 h at 250 rpm. To assess whether yeast nutrients were limiting, 100 g of fermented slurry was also incubated with 49 ml of buffer and 1 g of yeast extract. Figure 8 shows ethanol yields from the undiluted and diluted samples for each initial SLR trail. As can be seen, adding yeast extract along with 50 ml of water did not improve ethanol yields, thus indicating that nutrients were not limiting ethanol yields. Only a slight improvement in ethanol yield was noted when fermented material from the 25% solid loading rate trial was diluted and incubated an additional 72 h. No benefit was observed in the 27% solid loading rate trials. The only significant increase in ethanol yield was when 100 g of the 21% solid loading rate material was diluted with 10 ml of water and fermented 72 h more. Based on these findings it doesn't appear that water activity was the primary limiting factor. Instead we postulate that low enzyme activity may be the chief limitation, since residual sugar levels also remained low in these secondary fermentations of diluted samples. As noted by other investigators, a significant issue with cellulase enzymes in irreversible binding to biomass components [18, 19, 20, 21,22].
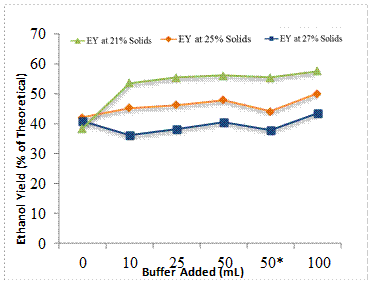
50*: 49 mL buffer+1 g of Yeast Extract
4. Conclusion
The goal of this project was evaluate fed-batch, solid state, simultaneous saccharification and fermentation (SSF) as an approach to reduce enzymes used in converting cellulose to ethanol and to increase then solids loading to maximize ethanol titer. During fed-batch submerged SSF of kraft pulp there were no significant differences between the final ethanol concentrations (47-52 g/l) or yield (77-83%) when enzyme dosages were reduced from 133% to 33% of the average dosage calculated from the literature. It was possible to achieve a solids loading rate of 14% and still maintain adequate mixing.
During fed-batch saccharification trials in solid state bioreactor, 34.8% solids loading was achieved with an acceptable mixing rate, while reducing enzyme dosage to 19% of the literature average. Due to feedback inhibition of enzymes, however, glucose levels only reached ~100 g/L, which was 35% of the theoretical yield. To prevent feedback inhibition [4, 5] fed-batch SSF trials were conducted under identical conditions. Due to apparent yeast inhibition caused by low water activity [4], the ethanol yield only rose to 20% of theoretical, while glucose levels rose to 70 g/L. We then evaluated performance at solid loading rates of 21, 25, and 27% and ethanol yields increased to 42-44%, confirming that low water activity was at least partially responsible for low ethanol yields. However, in comparison to a submerged SSF trial at 14% SLR, we observed a 37% loss of ethanol from the solid state reactor due to evaporation. We also detected substantial levels of unhydrolyzed cellulose in these trials. We then further diluted the fermented slurry and conducted a secondary fermentation. This did not substantially improve ethanol yields or cellulose hydrolysis, suggesting that enzyme inactivation via irreversible binding may be responsible [18, 19, 20, 21, 22].
References
[1] P.A. Gibbs, R.J. Seviour, F. Schmid. 2000. Growth of Filamentous Fungi in Submerged Culture: Problems and Possible Solutions. Critical Reviews in Biotechnology, 20:17-48. View Article
[2] M.J. Zhang, F. Wang, R.X. Su, W. Qi, Z.M. He. 2009. Ethanol Production from High Dry Matter Corncob using Fed-batch Simultaneous Saccharification and Fermentation after Combined Pretreatment. Bioresource Technology, 101:4959-64. View Article
[3]. L.R. Lynd, W.H. van Zyl, J.E. McBride, M. Laser. 2005. Consolidated bioprocessing of cellulosic biomass: an update. Current Opinion in Biotechnology, 16:577-583. View Article
[4] R.C. Kuhad, G. Mehta, R. Gupta, K.K. Sharma. 2010. Fed batch Enzymatic Saccharification of Newspaper Cellulosics Improves the Sugar Content in the Hydrolysates and Eventually the Ethanol Fermentation by Saccharomyces cerevisiae. Biomass Bioenergy, 34:1189-94. View Article
[5] B. Erdei, Z. Barta, B. Sipos, K. Reczey, M. Galbe, G. Zacchi. 2010. Ethanol Production from Mixtures of Wheat Straw and Wheat Meal. Biotechnology for Biofuels, 3:1-9. View Article
[6] L. Camacho-Ruiz, N. Perez-Guerra, R.P. Roses 2003. Factors Affecting the Growth of Saccharomyces cerevisiae in Batch Culture and in Solid State Fermentation. Electronic Journal of Environmental, Agricultural and Food Chemistry, 2:531-542. View Article
[7] A. Pandeya, C.R. Soccola, D. Mitchell. 2000. New Developments in Solid State Fermentation: I-Bioprocesses and Products. Process Biochemistry, 35:1153-1169. View Article
[8] X.Y. Zhang, H. Mo, J. Zhang, Z.H. Li. 2003. A Solid-State Bioreactor Coupled with Forced Aeration and Pressure Oscillation. Biotechnology Letters, 25:417-20. View Article
[9] C. Moukamnerd, M. Kino-oka, M. Sugiyama, Y. Kaneko, C. Boonchird, S. Harashima, H. Noda, K. Ninomiya, S. Shioya, Y. Katakura. 2010. Ethanol Production from Biomass by Repetitive Solid-State Fed-Batch Fermentation with Continuous Recovery of Ethanol. Applied Microbiology and Biotechnology, 88:87-94. View Article
[10] W.R. Gibbons, C.A. Westby, T.L. Dobbs. 1986a. Intermediate-scale, Semicontinuous Solid-phase Fermentation Process for Production of Fuel Ethanol from Sweet Sorghum. Applied Environmental Microbiology, 51:115-22. View Article
[11] W.R. Gibbons, and C.A. Westby. 1986b. Effect of Pulp pH on Solid Phase Fermentation of Fodder Beets for Fuel Ethanol Production. Biotechnology Letters, 8:657-662. View Article
[12] C. Karunanithy, K. Muthukumarappan, W.R. Gibbons. 2013. Effect of extruder screw speed, temperature, and enzyme levels on sugar recovery from different biomasses. ISRN Biotechnology, DOI:10.5402/2013/942810. View Article
[13] N.A. Bauer, and W.R. Gibbons. 2012. Saccharification versus Simultaneous Saccharification and Fermentation of Kraft Pulp. International Journal of Agricultural and Biological Engineering. 5:48-55. View Article
[14] E. Tomas-Pejo, M. Ballesteros, J.M. Oliva, L. Olsson. 2010. Adaptation of the Xylose Fermenting Yeast Saccharomyces cerevisiae F12 for Improving Ethanol Production in Different Fed-batch SSF Processes. Journal of Industrial Microbiology and Biotechnology, 37:1211-20. View Article
[15] M. Ballesteros, J.M. Oliva, P. Manzanares, M.J. Negro, I. Ballesteros I. 2002. Ethanol Production from Paper Material using a Simultaneous Saccharification and Fermentation System in a Fed-batch Basis. World Journal of Microbiology and Biotechnology, 8:559-61. View Article
[16] C.M. Rochel, C.J. Dibble, J.J. Stickel. 2009. Laboratory-scale Method for Enzymatic Saccharification of Lignocellulosic Biomass at High-solids Loadings. Biotechnology for Biofuels, 2:1-11. View Article
[17] H. Jorgensen, J. Vibe-Pedersen, J. Larsen, C. Felby. 2007. Liquefaction of Lignocellulose at High-solids Concentrations. Biotechnology and Bioengineering, 96:862-70. View Article
[18] A.D. Eckard, K. Muthukumrarappan, W.R. Gibbons. 2011. Pretreatment of Extruded Corn Stover with Polyethylene Glycol to Enhance Enzymatic Hydrolysis: Optimization, Kinetics, and Mechanism of Action. BioEnergy Research. 5: 424-438. View Article
[19] A.D. Eckard, K. Muthukumrarappan, W.R. Gibbons. 2012a. Analysis of Casein Biopolymers Adsorption to Lignocellulosic Biomass as a Potential Cellulase Stabilizer. Journal of Biomedicine and Biotechnology, 1:1-11. View Article
[20] A.D. Eckard, K. Muthukumrarappan, W.R. Gibbons. 2013a. Enzyme Recycling in a Simultaneous and Separate Saccharification and Fermentation of Corn Stover: A Comparision between the Effect of Polymeric Micelles of Surfactants and Polypeptides. Bioresource Technology, 132:202-209. View Article
[21] A.D. Eckard, K. Muthukumrarappan, W.R. Gibbons. 2012b. Modeling of Pretreatment Condition of Extrusion Pretreated Prairie Cordgrass and Corn Stover with Poly (oxyethylen (20) Sorbitan Monolaurate. Applied Biochemistry and Biotechnology, 167: 377-393. View Article
[22] A.D. Eckard, K. Muthukumrarappan, W.R. Gibbons. 2013b. Enhanced Bioethanol Production from Pretreated Corn Stover via Multi-positive Effect of Casein Micelles. Bioresource Technology, 135:93-102. View Article