Volume 1, Year 2014 - Pages 16-26
DOI: 10.11159/jbb.2014.003
Ash Analysis of Poultry Litter, Willow and Oats for Combustion in Boilers
Bimal Acharya, Animesh Dutta, Shohel Mahmud, Mohammad Tushar, Mathias Leon
School of Engineering, University of Guelph, 50 Stone Rd E, N1G 2W1, ON, Canada
Abstract - The large content of potassium and chlorine in lignocellulosic biomass greatly enhances the formation and accumulation of deposits and thus lead to corrosion in the different component of boilers compared to that of coal fired boiler. It is, thus, imperative to study the characteristics of the ash from lignocellulosic biomass and compare the results with the ash of non-lignocellulosic biomass. In this study, two lignocellulosic biomass ash samples from oat (agricultural biomass) and willow (forest wood biomass) were prepared and characterized and compared with a non-lignocellulosic biomass (poultry litter) ash samples. The detailed ash analysis and characterization of biomasses were performed by using elemental analysis, scanning electron microscopy (SEM) and X-ray diffraction (XRD). Ash samples from these biomasses are prepared at 800ᴼC, 900ᴼC and 1000ᴼC for SEM and XRD analysis. The poultry litter ash exhibits a higher alkali index, clorine and sulfur content, and a lower ash fusion temperature and silica in ash compared to that of willow and oats. Also, a very high ash content in poultry litter potentially requires high-volume ash-handling equipment and more attention to particulate removal, slagging, and fouling while used in a combustor/boiler. Therefore, care must be taken for using poultry litter as fuel for coal or lignocellulosic biomass combustion system.
Keywords: Ash, Lignocellulosic and non-lignocellulosic biomass, SEM, XRD, Alkali indices.
© Copyright 2014 Authors - This is an Open Access article published under the Creative Commons Attribution License terms. Unrestricted use, distribution, and reproduction in any medium are permitted, provided the original work is properly cited.
Date Received: 2013-11-15
Date Accepted: 2014-05-13
Date Published: 2014-09-30
1.Introduction
Biomass can substitute the fossil fuels for generating power from boilers to reduce the Green House Gas (GHG) emission. The large alkali content of lignocellulosic biomass especially from the agricultural crop family causes more deposits and corrosion effect on the different components of boiler than the coal fired boiler [1-9]. This ultimately limits the operating temperature of the boiler shown in Table 1. Besides potassium and chlorine, large contents of calcium and silica in the lignocellulosic biomass cause deposit formation in the boiler. During agricultural biomass combustion, it is found that the bottom ash contains 34-84 % of potassium and calcium silicate components [10] whereas flue gas filter contains aerosols rich in KCl and K2SO4, which are formed when the flue gas is cooled down to 700-800C [11]. The fly ash contains mostly potassium and chlorine components in the range of 44 to 84% [11]. The rate of ash deposit formation on boiler heat transfer surfaces increases when the portion of the biomass ash is liquefied or melted. This phenomena may be caused due to a lower melting temperature of the ash because of the presence of the components shown in the Table 1. With the presence of components listed in the Table 1, the melting temperature could potentially start from 350°C, which is too low for a commercial combustion system to produce energy. During the agricultural straw combustion, boiler deposit contains large concentrations of K and Cl in addition to some silica, calcium and sulphur [12]. In the agriculture residue fired boiler, corrosion is a severe problem because of the reaction by KCl with the metal parts of boiler coils. Montgomery et al [13] observed the corrosion rates 0.8mm/Khrs, 0.3mm/Khrs and 0.02 mm/Khrs at steam temperatures of 570°C, 530°C and 440°C respectively. The corrosion mechanisms in the agricultural residue fired boiler is not yet completely understood [14, 15]. However, it is understood that sulfation of potassium chroride near the metal surface generates HCl gas or Cl2 gas that reacts with the boiler coils, and removing of Fe and Cror corrosion can be due to release of Cl2 gas after the reaction between KCL and Fe2O3 [16]. Therefore, for designing any types of biomass fired boiler, it is necessary to have an in depth knowledge on the deposition and corrosion formation and its effect on the every component of the boiler especially heating coils so that the steam temperature can be raised to make more efficient energy conversion system. Even though there are a number of study on ash analysis of other biomasses are performed [3, 5, 17], knowledge of the detailed analysis of different lignocellulosic and non-lignocellulosic biomass of Ontario has not yet been carried out. Hence, this study focuses to analyze ash samples of oats from agricultural family, willow from wood family, and poultry litter from non-lignocellulosic family by lab analysis, scanning electron microscopy (SEM) and X-ray diffraction (XRD) for their potential application as a fuel in combustion systems.
Table 1. Melting temperature of different components of biomass [3]
Components | Minimum Melting Temperature °C |
KCl | 774 |
K2SO4 | 1059 |
K2O +SiO2 | 750 |
K2O.4SiO2 +CaO.SiO2 | 740 |
KCl + K2SO4 | 694 |
KCl + FeCl2 | 355 |
KCl + K2SO4+Fe2O3 | 577 |
2. Materials and Methods
2.1 Sample Collection
Willow and oats samples were collected from the University of Guelph research center, and non-lignocellulosic sample of poultry litter was collected from a Poultry farm in Willington, Ontario. Willow and Oats were collected in the form of stem and pellets. Poultry litter was collected in the form of a mixture of manure (excreta), feathers, feed, dead birds, broken eggs, and bed material (wood shavings or straw). These samples were chopped in smaller pieces and grinded.
2.2 Sample preparation
Ash samples were prepared by a muffle furnace, and a custom designed Quartz Wool Matrix (QWM) reactor shown in Figure 1 at 800°C, 900°C and 1000°C. A detailed description of this reactor is available at (Acharya and Dutta 2013) (18). The reactor consists of a Stainless Steel (SS) tube heated by four electric heaters of 1.25KW capacity in close contact with the reactor wall and separately controlled by two PID controllers. The SS tube has an inner diameter of 75 mm and height of 600 mm. This reactor allows simulation of any gas-solid relative velocity; gas composition and gas temperature in a reactor while a precision electronic balance continuously measures the mass change of a reaction. Such reactor could thus accurately simulate conditions one would expect in a fixed, moving or entrained flow reactor. Before starting an experiment, the reactor was heated until an equilibrium temperature or steady state is attained. Temperatures were measured at two different locations one from upper mid portion of reactor and another from lower mid portion of the reactor by two separate thermocouples through the temperature controller (CNi16D, Temperature and Process Controller, Omega, USA). Then the sample of biomass of known mass and moisture content were placed into the reactor and air is supplied. The electronic balance (Model: MS204S, Mettler Toledo, Switzerland) continuously measured the mass of the biomass. When the weight of sample at a specific temperature reached a constant value, it is assumed that the combustion is completed. Thereafter, the sample is cooled down in desiccator and weighed. Its composition is analyzed by SEM and XRD techniques.
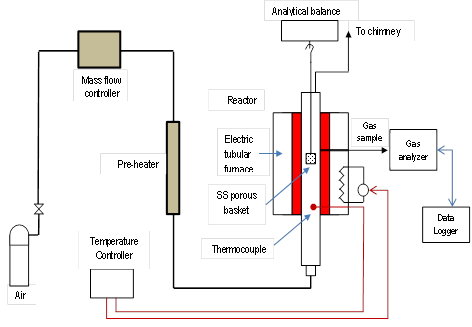
2.3 Methods of Analysis
Ultimate analysis of the raw biomass samples was carried out according to ASTM D 5373-08 method. All samples were dried at 105°C for 24 hours prior to the experiment for Ultimate analysis. During the experiment, the combustion was carried out at 925°C under Helium atmosphere while the reduction was carried out at 650°C. Ultimate analysis of biomass sample provides the elemental analysis of C, H, O, S and N. Methods and equipment used and results are listed in Table 2.
Table 2. Methods and Equipment used in characterizing raw biomass samples
*MC=Moisture Content; AC=Ash Content; VM=Volatile Matter; FC=Fixed Carbon; C=Carbon; H=Hydrogen; N=Nitrogen; S=Sulphur; O=Oxygen
Proximate Analysis | Ultimate Analysis | Higher Heating Value(HHV) | ||||||
Parameter | MC | AC | VM | FC | C, H, N | S | O | HHV |
Method | ASTM E871 | ASTM E1755 | ASTM D3175 | ASTM E872 | ASTM D5375 | ASTM D4239 | ASTM E870 | ASTM E711 |
Equipment Used | Muffle Furnace | Muffle Furnace | Muffle Furnace | Calculated Value | Leco CHN-1000 Elemental Analyzer | Leco SC-432 Elemental Analyzer | Calculated Value | C-200 Bomb Calorimeter |
Morphology of the biomass samples were analyzed using SEM at the lab facility of University of Guelph. Samples were coated with gold (20 nm) with a sputter coater (Model K550; Emitech, Ashford, Kent, England) prior to SEM analysis. SEM micrographs were taken by using a model S-570 (Hitachi High 115, Technologies Corp., Tokyo, Japan) at 10 kV accelerating voltage. Images were captured by extracting electrons from a sharp tungsten tip, and formed into a fine beam by a series of electromagnetic lenses. Resolutions of up to one nanometer was able to produce.
X-Ray diffraction test was carried out on the ash samples of the biomass at the lab facility of University of Guelph. The XRD test has given all the constituent elements, minerals and ores present in the ash. This technique is used to understand the crystal structure, chemical composition and physical properties of ash materials and thin films.. A comprehensive database of all known elements, minerals and ores were used to search for diffractogram patterns. Powder X-ray diffraction patterns (XRD) for various sample of ashes were collected in Bragg-Brentano geometry at room temperature on a STOE goniometer using the Cu Kα radiation (λ = 1.5406 Å) produced by an ENRAF-NONIUS
FR571 rotating anode generator. A Moxtek 2500 Silicon drift energy sensitive detector was used in order to minimize the background level. The patterns were measured in the 2θ interval from 5° to 70°, with a step size of 0.02° and 24 s counting time per step.
3. Results and Discussions
3.1 Chemical Analysis
Ultimate and proximate analyses of each sample were conducted as per the ASTM standard and is shown in Table 3. It is observed that lignocellulosic biomass contains more carbon and oxygen components 52.2% & 34.0% in oats and 50.7% & 24.1% in willow than poultry litter with 43.3% & 6.0%. But Poultry litter has significantly high Nitrogen and Ash content, and moderately high Sulfur content than willow and oats. This is likely to present some challenges when using poultry litter in a combustion device designed for lignocellulosic biomass. In addition, a lower volatile matter and a higher moisture contents in poultry litter compared to lignocellulosic biomass may cause problems in establishing flame in the combustor.
Table 3. Analysis of raw oats, poultry litter and willow (wt%, dry basis)
Ultimate Analysis | |||
Elements | Oats | Poultry Litter | Willow |
Carbon, % | 52.2 | 43.3 | 50.7 |
Hydrogen, % | 6.6 | 6.6 | 5.9 |
Oxygen, % | 34.0 | 6.0 | 24.1 |
Nitrogen, % | 0.6 | 5.7 | 0.5 |
Sulgur, % | 0.3 | 1.2 | 0.4 |
Ash Contents | 22.3 | 11.5 | 5.6 |
Proximate Analysis | |||
Moisture (%) | 7.7 | 20.1 | 5.2 |
Volatile Matter (%) | 74.3 | 54.3 | 73.2 |
Fixed Carbon (%) | 12.3 | 3.3 | 10.2 |
HHV | 16.4 | 10.1 | 16.1 |
3.2 Chlorine and Ash Fusion Temperature
Samples were tested for Chlorine and ash fusion temperature by burning it as per the guideline of ASTM standard. The results of the analysis is shown in Table 4. Out of tested three samples, only poultry litter contains very small amount of sulfur. Lignocellulosic biomass samples of willow and oats have higher ash initial deformation temperature 1115°C and 1279°C than non-lignocellulosic biomass Poultry litter at 1048 °C and will be a better fuel than that of poultry litter. Also, the high ash content in poultry litter may require high-volume ash-handling equipment and more attention to particulate removal, slagging, and fouling while used in a combustor/boiler.
Table 4. Chlorine & ash fusion temperature of poultry litter, willow and oats
Particular | Poultry Litter | Willow | Oats |
Chlorine (%) | 0.1 | 0 | 0 |
Ash Fusion Temperature (°C) | |||
Initial Deformation (IT) (°C) | 1048 | 1115 | 1279 |
Softening Temperature (ST) (°C) | 1074 | 1171 | 1303 |
Hemispherical Temperature (HT) (°C) | 1207 | 1258 | 1338 |
Fluid Temperature (FT) (°C) | 1240 | 1292 | 1354 |
3.3 Elemental Analysis of Ash
3.3.1 Calculations of Combustion Indices
To estimate the slagging, fouling and bed agglomeration potential of these three forms of biomass, alkali index (AI), the base-to-acid ratio (R b/a ), and the bed agglomeration index (BAI) are calculated using the procedure described by Vamvuka and Zografos [19, 20] as per Eqns. 1-3. When the AI values are within the range of 0.17 to 0.34 kg GJ -1 ([19], fouling or slagging may or may not occur, but it is certain to happen when the values are above this range. When the ratio of R b/a increases, the fouling tendency of a fuel ash increases. Also it is reported that bed agglomeration occurs when BAI values are lower than 0.15 [19]
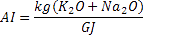


Table 1. Elemental Analysis of Poultry Litter, Willow and Oats in % Ash basis
Components | Poultry Litter | Willow Pellets | Oat Pellets |
SiO2 | 2.69 | 67.77 | 60.68 |
TiO2 | 0.02 | 0.44 | 0.61 |
Al2O3 | 0.31 | 9.47 | 15.62 |
Fe2O3 | 0.57 | 2.89 | 0.4 |
MnO | 0.33 | 0.11 | 0.09 |
CaO | 65.17 | 9.4 | 5.59 |
K2O | 6.36 | 3.53 | 9.85 |
Na2O | 2.48 | 2.44 | 0.47 |
P2O5 | 17.46 | 1.74 | 4.54 |
Cr2O3 | 0.03 | 0.03 | 0.07 |
Alkali Index (AI) | 1.81 | 0.42 | 0.35 |
Base to Acid Ratio (Rb/a) | 26.2 | 0.50 | 0.24 |
Bed Agglomeration Index (BAI) | 0.06 | 0.48 | 0.04 |
As shown in Table 5, the elemental ash analysis of poultry litter contains 65.17% and 17.46% of CaO and P2O5, respectively. These values are 9.4% and 5.59% and 1.74% and 4.54% for willow and oats, respectively. Lignocellulosic biomass willow and oats contains more than 60% of SiO2. Willow contains 20.7% of MgO and 9.47% of Al2O3 whereas oats contains 15.62% of Al2O3 and 9.85% of K2O. The major compounds in poultry litter identified in the ash are CaO (65%), P2O5 (17.5%) and K2O (6.4%), which falls into the category of biomass ash rich in calcium, phosphorous, and potassium. As can be seen from combustion indices, Poultry litter is expected to have more corrosion and deposit formation compared to other two samples of lignocellulosic biomass. This is because the concentration of alkali metals (Na2O, and K2O) is higher in poultry litter than in willow and oats, indicating that poultry litter is a more challenging fuel than lignocellulosic biomass. High alkali content, especially in conjunction with high chloride levels, results in a high potential for slagging, fouling, particulate emissions, and corrosion during combustion [15-17, 21-22]. This is one of the reasons for having a lower ash fusion temperature for poultry litter than that of willow and oats.
Silica salts formed by K and Na show strong tendencies to become sticky and form slag on the hot surfaces of the combustion equipment and the boiler. Maintaining low combustion temperatures will also help in controlling alkali-related slagging and fouling problems. Fluidized bed combustors offers this advantage vis-à-vis conventional (fixed/moving bed) combustors as they typically operate in the range of only 800-900°[17].
3.4 SEM tests
The presence of potassium and chlorine in the fuel significantly increases the deposit formation and corrosion potential in combustion devices, compared to coal. It is known that the alkali species which cause the bed agglomeration come from the fuel ash [2, 3, 5, 12-17]. Hence, it is important to understand the behavior of alkali species in ash for the formation mechanisms of agglomerates and coating layers. In this study, ash samples are prepared at 800°C, 900°C and 1000°C and scanning electron microscopy imagery has been performed on the ash samples.
3.4.1 Poultry Litter
As shown in Figures 2 (a-c), the course mode particles has an irregular surface structure. The temperature during the process has not been high enough for complete coalescence of the ash into spherical particles. Some of the particles are long, fiber-like agglomerates still resembling the original wood fiber structure [12, 17]. The surfaces of the sample particles are generally formed by primary particles, which are less than few micrometers in size. These consequently joined together and form chain like structure. The primary particles are mainly found as mixture of round shaped and crystalline structures. The ash particle does not contain much unburned particles at higher temperature. At low temperature, the sample contains some wool like structures, which gradually disappears with the increase in combustion temperature. This wool like structures are not combustible at low temperature and can only be combusted at high temperature [16-17]. Also at high temperature, particles become more brittle as the minerals matters in the form of crystal increases. Hence the particles become smaller and many cracks start to show up as the combustion temperature increases. The increase in smooth surfaces in the samples with the increase in combustion temperature also supports the relative increase in mineral matters in the samples which is obtained in XRD analysis.
![]() |
![]() |
![]() |
(a) | (b) | (c) |
Skrifvars et al. (1998)[11] characterized the sintering tendency of ten biomass ash samples and classified the ash components into three groups: simple alkali salts, silicates and the rest non-melt. The fusible compounds melt and coat the surface of ash particles during combustion. The EDS spot analyses indicate that these melts, which are alkali silicates, are rich in K or Na. Based on the K2O־CaO־SiO2 phase diagram and the Na2O־SiO2 and K2O־SiO2 phase systems [21], the melting point of these alkali silicates are in the range of 800 - 1200°C. These alkali silicates formed during combustion can melt and form a sticky coating on the surface of ash particles, or on silicon dioxide grains, used as bed material in fluidized bed combustors at high temperature, leading to agglomeration.
Large and small sized ash particles may play different roles in bed agglomeration. When small-sized ash particles collide with the bed particles, the molten alkali species on them will be transferred to the surface of the bed particles. Large-sized ash particles may increase the amount of melts on local surface of bed particle and may act as the necks for the agglomerate formation. Bed agglomeration can be controlled by keeping the bed alkali contents low enough by regularly discharging the bed ash and feeding fresh sand into the bed [22].
3.4.2 Willow
Figure 3 (a), (b) and (c) show the images of the Willow' ash samples at 800, 900 and 1000°C respectively. As we have seen in poultry litter, at low temperature, the sample contains some wool like structures which gradually disappears with the increase in combustion temperature [2, 16]. The surface has irregular structure which signifies the process has not been enough for complete coalescence of the ash into spherical particles. Some of the particles were long, fiber like agglomerates still resembling the original wood fiber structure. The surfaces of the particles were usually formed in small sizes which had often sintered together forming chain-like agglomerate structures [2-3,17]. The primary particles were mainly cotton shaped but also cornered ones were seen like crystalline structure. This signifies, the ash particles does not contain significant amount of unburned samples. Also at high temperature, particles become more brittle as the minerals matters in the form of crystal increases. Hence the particles become smaller and many cracks start to show up as the combustion temperature increases. Because of the presence of high Silicon dioxide, Magnesium dioxide and other alkalis, the structure contains smooth surface which represents the presence of metallic components in the ash sample. The increase in smooth surfaces in the samples with the increase in combustion temperature also supports the relative increase in mineral matters in the samples which is obtained in XRD analysis.
![]() |
![]() |
![]() |
(a) | (b) | (c) |
3.4.3 Oats
Figure 4 (a), (b) and (c) show the images of the Oats ash samples at 800, 900 and 1000°C respectively. At low temperature, the sample contains some wool like structures which gradually disappears with the increase in combustion temperature. This broken wood like structures is not combustible at low temperature and can only be combusted at high temperature [16-17]. Similar to willow ash, some of the particles were long, fiber like agglomerates still resembling the original Oats fiber structure. At 900˚C, the ash metallic components are formed and hole like spots are observed. The primary particles were mainly cotton shaped but also cornered ones are seen like crystalline structure. This signifies, the ash particles does not contain significant amount of unburned samples. Also at high temperature, particles become more brittle as the minerals matters in the form of crystal. Hence the particles become smaller and many cracks start to show up as the combustion temperature increases. Because of the presence of high Silicon dioxide, Magnesium dioxide and other alkalis, the structure contains smooth surface which represents the presence of metallic components in the ash sample. The increase in smooth surfaces in the samples with the increase in combustion temperature also supports the relative increase in mineral matters in the samples which is also obtained from ash analysis.
![]() |
![]() |
![]() |
(a) | (b) | (c) |
3.5 XRD tests(Crystalline Phases Detected by Powder Diffraction)
The XRD tests provide all the constituent elements, minerals and ores present in the ash. The main purpose of the XRD tests was to determine the minerals present in the ash sample that could have potential effect on slagging, corrosion, fouling and agglomeration.
3.5.1 Poultry Litter
According to the researchers the major components for the poultry litter are struvite, sylvite, calcite, Weddellite and quartz [24-27]13-27]. Figure 5 shows the XRD patterns for poultry litter ash prepared at temperatures 800, 900 and 1000°C. The peaks at 17, 28, 33 2θ as can be seen from the Fig 5 represents the crystalline structure of struvite (NH4MgPO4·6H2O) [24-27], which with the increase in temperature, the height of the peak increases. This can be attributing to the increase in relative amount of crystalline structure in the sample with the increase in combustion temperature. Fig 5 also shows that there is a small peak of quartz (SiO2) at 26 2θ [26]. Sylvite (KCl) is identified in the samples at 28, 29, and 51 2θ [24, 27]. Calcite (CaCO3) and Weddellite (CaC2O4·2H2O) were also identified by the powder XRD at 31, 34 [27] and 43, 46 [26] 2θ respectively. Calcium, being an important diet for the poultry, can be expected to show as some kind of crystalline structure of calcium compound in the litter samples.
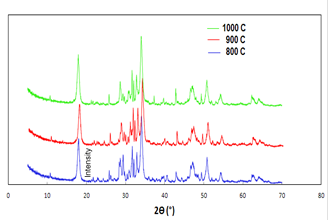
3.5.2 Willow and Oats
The XRD analysis (Figure 6) confirm that the basic forms in both willow and oats ash are SiO2, CaSO4 and K2Ca(CO3) 2, which determine the nature of the alkaline extracts in water and Willow ash. The ash fusion temperature of willow and oats are about 1100-1300°C, and 1250-1350°C respectively. This range of temperature limits the operating temperature of the combustor of a boiler system. The peaks of biomass are in the range of 20-40, 2θ which may be due to presence of arcanite, periclase, quartz, calcium silicate and potassium iron oxide in the molten biomass [28]. The XRD patterns of oat ash prepared at different experimental conditions showed hump for all three samples starting from 2θ=15 ־ 35° with some sharp peaks near 30°. These patterns demonstrate that oat ash is mainly amorphous in nature consists of majorly silica [29]. The sharp peak at 2θ=29° for the ash produced at 800°C is due to the presence of K2SO4. However, this peak diminishes with the increase in temperature and a new peak at 2θ=28° for KAlSiO4 becomes visible at 1000°C [30].
![]() |
![]() |
(a) XRD of willow ash | (b) XRD of oats ash |
4. Conclusions
The poultry litter has very high ash content, and exhibits higher alkali index, lower ash fusion temperature, higher Cl and sulfur content, lower silica in ash compared to that of willow and oats. . Therefore, care must be taken for using poultry litter as fuel for combustion system. Also, the high ash content in poultry litter may require high-volume ash-handling equipment and more attention to particulate removal, slagging, and fouling while used in a combustor/boiler. The ashes from the samples studied contain a significant amount of Silica and Calcium and can be used for the cement production. Thick deposit of the ash prevents heat flow on the boiler so regular disposal of ash from the boiler is required in any biomass fired boilers. It is recommended to use regular soot blower and thus obtain better heat transfer.
References
[1] Acharya, B., Dutta, A., & Basu, P. (2012). Circulating-Fluidized-Bed-Based Calcium-Looping Gasifier: Experimental Studies on the Calcination-Carbonation Cycle. Industrial & Engineering Chemistry Research, 51(25), 8652-8660. View Article
[2] Baxter, L. L.; Miles, T. R.; Miles, T. R., Jr.; Jenkins, B. M.; Milne, T.; Dayton, D.; Bryers, R. W.; Oden, L. L. The Behavior of Inorganic Material in Biomass-Fired Power Boilers: Field and Laboratory Experiences. Fuel Process. Technol. 1998, 54, 47-7 View Article
[3] Jensen,P.A., Flemming J. Frandsen, Jørn Hansen, Kim Dam-Johansen,Niels Henriksen, and Steffen Horlyck, (2004) SEM Investigation of Superheater Deposits from Biomass-Fired Boilers, Energy & Fuel 2004, 18, 378-384. View Article
[4] Roy M.M, Dutta,A., Corscadden, K.,. (2013). An experimental study of combustion and emissions of biomass pellets in a prototype pellet furnace, Applied Energy, Vol 108, pp. 298-307 (I.F. 5.106). (NSERC) View Article
[5] Kludze,H., Deen,B., Dutta, A. (2013). Impact of agronomic treatments on fuel characteristics of herbaceous biomass for combustion, Fuel Processing Technology, Vol. 109, pp 96-102 (I.F. 2.945). (OMAFRA) View Article
[6] Roy M.M.,, Dutta,A., Corscadden,K., Havard P.,and DickieL. (2011). Review of Biosolids Management Options and Co-incineration of a Biosolid-derived Fuel, Waste Management, 31 (11), pp. 2228-2235 [N-Viro, NSDA] (I.F: 2.358) View Article
[7] Jarungthammachote S.and Dutta A. (2012). Experimental investigation of multi-stage air-blow and air-steam gasification. in print Int. J Energy Res. 36 (3), 335-345. (I.F: 1.86) View Article
[8] Thamavithya, M., Jarungthammachote,S., and Dutta,A., and Basu. P. (2012). Experimental study on sawdust gasification in a spout-fluid bed reactor. Int. J Energy Res. 36 (2), 204-217. (I.F: 1.86) View Article
[9] Dhungana, A., Dutta,A., Basu,.P., 2012. Torrefaction of non -lignocellulose biomass waste, Cdn. J. of Chem. Engineering, 90 (1) 186-195. [NSERC] (I.F: 0.707)
[10] Frandsen, F., Nielsen, H. P., Hansen, L. A., Hansen, P. F. B. Andersen, K. H., Sørensen, H. S. (1998) Ash Chemistry Aspects of Straw and Coal-Straw Co-firing in Utility Boilers. Paper presented at the 15th Annual International Pittsburgh Coal Conference. PA, USA, September, 1998. View Article
[11] Christensen, K. A.; Stenholm, M.; Livbjerg, H. (1998). The Formation of Submicron Aerosol Particles, HCl, and SO2 in Straw-Fired Boilers. J. Aerosol Sci. 1998, 29 (4), 421-444. View Article
[12] Michelsen, H. P.; Frandsen, F.; Dam-Johansen, K.; Larsen, O. H. (1998). Deposit and High-Temperature Corrosion in a 10 MW Straw-Fired Boiler. Fuel Process. Technol. 1998, 54, 95-108. View Article
[13] Montgomery M., Karlson, A., Larsen, O. H. (2002). Field test corrosion experiments in Denmark with biomass fuels. Part 1: Straw firing. Mater. Corros. 2002, 53, 121-131. View Article
[14] Montgomery M., Biede, O. & Larsen, O. H. Corrosion Investigation at Maribo Sakskrbing c, Part I. Technical University of Denmark, Department of Manufacturing Engineering, 2001.
[15] Nielsen H. P. Frandse, F. J., Dam-Johansen K. & Baxter L. L. (2000). The Implication of Chlorine-Associated Corrosion on the Operation of Biomass-Fired Boilers. Prog. Energy Combust. Sci. 2000, 26, 283-298 View Article
[16] Hansen L. A., Nielsen H. P., Frandsen F. J., Dam-Johansen, K,. Horlyck S. & Karlsson A.(2000). Influence of Deposit Formation on Corrosion at a Straw-Fired Boiler. Fuel Process. Technol. 2000, 64, 189-209. View Article
[17] Skrifvars, B.-J., Sþris, G., Backman, R., Widegren-Dafgasrd, K. and Hupa, M. (1997) Ash behavior in a CFB boiler during combustion of Salix. Energy Fuels 11, 843-848. View Article
[18] Acharya B and Dutta A. "Characterization of Torrefied Willow for Combustion Application; Journal of Biobased Materials and Bioenergy, Volume 7, Number 6, December 2013 , pp. 667-674(8) View Article
[19] Vamvuka, D., Zografos,D. (2004) Predicting the behaviour of ash from agricultural wastes during combustion. Fuel 83 (2004) 14-15. View Article
[20] amvuka,D., Topouzi,V., S. Sfakiotakis, Evaluation of production yield and thermal processing of switchgrass as a bio-energy crop for the Mediterranean region. Fuel Process Technol. 91 (2010) 988-996. View Article
[21] Acharya, B., Sule, I. & Dutta, A. "A review on advances of torrefaction technologies for biomass processing. Biomass Conversion and Biorefinery (2012). Available at: http://www.springerlink.com/index/10.1007/s13399-012-0058-y. View Article
[22] Thy, P., Jenkins, B. M., Grundvig, S., Shiraki, R., Lesher, C. E. 2006. High temperature elemental losses and mineralogical changes in common biomass ashes. Fuel, 85(5), 783-795. View Article
[23] Barišić, V., Åmand, L. E., & Coda Zabetta, E. (2008). The role of limestone in preventing agglomeration and slagging during CFB combustion of high phosphorus fuels. World Bioenergy, Jönköping (Sweden), May 27 - 29.
[24] Güngör, K., Jürgensen, A., & Karthikeyan, K. G. 2007. Determination of phosphorus speciation in dairy manure using XRD and XANES spectroscopy. Journal of environmental quality, 36(6), 1856-1863. View Article
[25] Sen, A. N., Miller, L., Basu, P., & Dutta, A. (2003). Revamping of 4 x 58 MWth Pulverized Coal-Fired Boilers With Circulating Fluidized Bed Firing. ASME.
[26] Hunger, S., Sims, J. T., Sparks, D. L. 2008. Evidence for struvite in poultry litter: effect of storage and drying. Journal of environmental quality, 37(4), 1617-1625. View Article
[27] Zhang, S. Q., Zhang, F. D., Liu, X. M., Wang, Y. J., Zou, S. W., & He, X. S. 2005. Determination and analysis on main harmful composition in excrement of scale livestock and poultry feedlots. Plant Nutr Fert Sci, 11(6), 822-829. View Article
[28] Naik, S., Goud, V. V., Rout, P. K., Jacobson, K., & Dalai, A. K. (2010). Characterization of Canadian biomass for alternative renewable biofuel. Renewable energy, 35(8), 1624-1631. View Article
[29] Cheah, C. B., & Ramli, M. (2014). The fluid transport properties of HCWA-DSF hybrid supplementary binder mortar. Composites Part B: Engineering, 56, 681-690. View Article
[30] Niu, Y., Tan, H., Wang, X., Liu, Z., Liu, H., Liu, Y., & Xu, T. (2010). Study on fusion characteristics of biomass ash. Bioresource technology, 101(23), 9373-9381 View Article